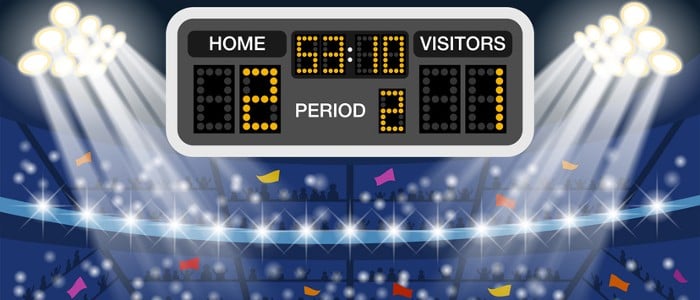
Production reporting is about the data
I’m a big believer in measuring what you want to improve. Measuring gives you data and you’ll see trends (good or bad) emerge. Figure out what is causing the good trends and keep doing that. Maybe you can even find ways to make the good trends better. Figure out what is causing the bad trends and find ways to stop doing that; or at least, minimize it.
I can’t imagine anyone arguing with the logic stated above, yet most companies I work with don’t observe trends and act accordingly. In fact, they are nowhere close to doing this. They manage with emotion: “This process feels right,” “I think that is a good employee,” “This job is a real money loser,” etc. I’m not against emotion when it comes to evaluating a process, employee, or job; I’m against only using emotion. Feelings should be developed based on data, and feelings should fill the gaps where it’s impractical – or impossible – to have data. For example, how many pieces an employee produced in an hour is data, but your perception of the employee’s attitude is a feeling. This is a balanced, appropriate look at an employee.
Related: Manufacturing Process Improvements That Make an Impact
Related: 6 Shop Floor Management Techniques Learned From 30 Years of Experience
So, the need for data is based on sound logic. But many companies don’t follow the logic. Why does this condition exist? It’s culture. If a company is running without the proper data and they are successful, that success reinforces the bad habit of not having data. This could go on for years, constantly reinforcing the bad habit and forming the culture. Once it’s part of the culture, it’s hard to change because people don’t like change. Change is unsettling; people like consistency.
Do you have the right tools to solve your data problem? We can discuss.
This can’t go on forever though. Eventually, the lack of data catches up with companies. It manifests itself in declining on-time delivery, quality, revenue, or profit. These bad trends help management focus on what had been there all along: a lack of data.
Enter the Manufacturing Production Report
Fix the lack of data by creating a Weekly Manufacturing Production Report.
What is a manufacturing production report?
A weekly production report shows how efficiently things are being built.
The report is broken down into two categories per employee: direct time and indirect time. On the direct side, efficiency is calculated by comparing the time it should take an employee to complete work to how long it actually took (estimated time/actual time = efficiency). In other words, when the employee was performing a direct labor task, how well were they doing? Did the task take more or less time than was expected? If it took more time, the efficiency is less than 100%; if it took less time, it is greater than 100%.
On the indirect side, how much indirect time did the employee have compared to their budget? In most cases, employees aren’t involved in direct labor activities the entire day. For example, it’s common to allow employees 15 minutes at the end of a shift for “clean-up” activities. If that was the only budgeted indirect time, each employee would have 1.25 hours of budgeted indirect per week. Their total reported indirect is compared to the budget, resulting in a positive, neutral, or negative variance.
The weekly detail of direct and indirect time is summarized for each employee. The summaries are rolled up to departments. Departments are rolled up to supervisors. Supervisors are rolled up to the next level of management, all the way up the chain of command, and this information composes the Weekly Manufacturing Production Report.
If all you do is create this Weekly Manufacturing Production Report and distribute it every week, you will see it has zero effect on the plant’s performance. The magic isn’t the report, it’s what you do with the report. This entire process I’m about to describe is designed to help supervisors understand how the actions of their employees affect the department’s performance. It’s a “scoreboard” for the supervisors and employees. If there is no scoreboard, what is the motivation to improve? How does anyone know if changes help or hurt performance? How do employees know if they are doing better or worse? Seriously, what fun is it when there is no score? Sure, you don’t feel the pain of a loss, but you never experience the thrill of a win either. The scoreboard provides facts and that’s the goal – working with facts.
Download the ERP selection criteria checklist
Power BI Reporting & AnalyticsPower BI could revolutionize your business by turning your ERP data into clear insights. Want to see Power BI in action? |
How to use the Weekly Manufacturing Production Report
Engage supervisors in this process by having them provide weekly feedback to the person they report to. The feedback is pretty straightforward:
- For any department that falls below 100% efficiency, supervisors need to provide the top three reasons why. There may be a dozen reasons, but just focus on the top three.
- If more indirect time was reported than was budgeted for, explain why.
This feedback creates a list of what the business needs to focus on. You’ll find labor estimates that need to be revised, employees that need to be trained, procedures that need to be sharpened. Supervisors and managers are usually surprised by how much indirect time is reported and the whole experience is eye-opening for everyone. This is how companies use data to improve—they keep chipping away at issues to improve performance overall.
A word of warning: None of this is done to punish anyone. If upper management turns this data into a weapon, the magic goes away. It becomes confrontational, not instructional. Instead of becoming a solution to problems, it becomes another problem.
Some additional words of warning: This is a WEEKLY Manufacturing Production Report. Don’t try to be an overachiever and turn it into a Daily Manufacturing Production Report. There are a few reasons for this:
- Time – Having supervisors identify the top three reasons their efficiency wasn’t at 100% on a daily basis produces too many things to fix. Everyone gets overwhelmed and then nothing gets done because there is too much to do. The goal is to chip away at the issues every week. Slow and steady gets the job done.
- Focus – Daily reports are too small of a time frame. Perfection is not the goal; consistency and continuous improvement are the goals. Everyday, good and bad things happen on the shop floor. Gather up a week’s worth, and the significant issues rise to the top. Focus on those issues. Just as importantly, don’t focus on the less significant issues.
- Momentum – A one-inning baseball game would be boring. Nine innings create an ebb and flow to the game. Your team may be down by two runs in the third inning, but there are six innings left! Anything could happen! The same is true with production. Bad things can happen on a Tuesday, but there are still three more days to overcome it! Weekly reporting allows you to offer a more balanced picture of the work being done and build a positive momentum.
Download the 6 step guide to successfully implement ERP
The production report is part of a bigger picture
The purpose of this blog post is to introduce the high level concept of what should be in a Weekly Manufacturing Production Report. You may have some roadblocks that get in the way of doing this. For example, do you have standard rates for operations? Are you collecting labor data? Do you have one integrated system to keep all the data? Maybe you just don’t know where to start. Whatever the case, this is how Visual South helps companies. You can start with a free 30 minute conversation with me. I assure you, it won’t be a sales pitch.